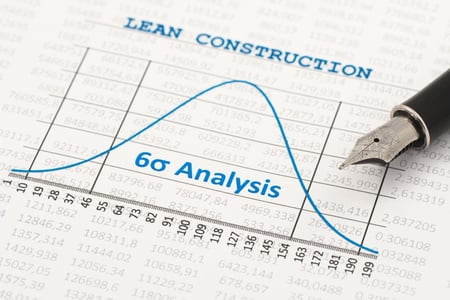
Three of the primary applications of lean production practices are:
1. Waste reduction Elimination of every conceivable source of waste in the production process to optimize resource allocation.
2. Process improvement Constant refinement of the production process with the goal of eliminating all steps that do not contribute to customer value creation.
3. Value stream mapping Consideration of how to contribute the most possible value to the customer and mapping the most efficient process for creating the value.
When you consider the effect of all three in combination, it is easy to understand the value of lean construction in creating winning bids. The result is the most cost-efficient proposal that is most likely to achieve... or exceed... the customer's expectations. Cimtas Module & Shipbuilding presents a great case study for this in its construction of the Izmit Bay Bridge which, when completed, will be the fourth largest suspension bridge in the world. By consistently applying lean practices, the company has outperformed its historic production rates and is exceeding customer expectations in managing the construction of a very complex project.
As we go about rebuilding America's infrastructure, lean manufacturing and production processes will likely be the key to long term productivity growth. Effective value stream mapping will readily reveal that state DOTs are facing budget cuts that will not allow them to replace their aging work force. Bidders that include technology solutions that reduce the cost of maintenance over the life of the asset will have a clear advantage over those that do not. As we wrote a year ago in Will precast manufacturers be ready for smart bridges?, the budget pressures on governments and recent technological advances are already moving us toward the construction of smart infrastructure.
This has started with utilization of bar codes and RFID tracking in inventory management systems for construction projects. Idencia itself was started as a product tracking system of this sort but we see this as only the beginning. Whereas static information about each product can presently be accumluated and tracked, future iterations of our solution will include sensors along with RFID tags so that the products themselves will be able to communicate dynamic information to the project owner. This evolution toward smart infrastructure will save the project owner time and the expense of human inspections.
About Idencia
Our purpose at Idencia is to offer precast RFID tracking solutions that improve productivity throughout the value chain. Our subscription offering applies to products from the time of manufacture through end-of-life. As a cloud-hosted product tracking system that is seamless between manufacturers, contractors and asset managers, Idencia adds information value to all, eliminates redundancy and saves time. If you would like to learn more, click below.

May 6, 2015 12:57:00 PM
Comments